Understanding Configure to Order (CTO)
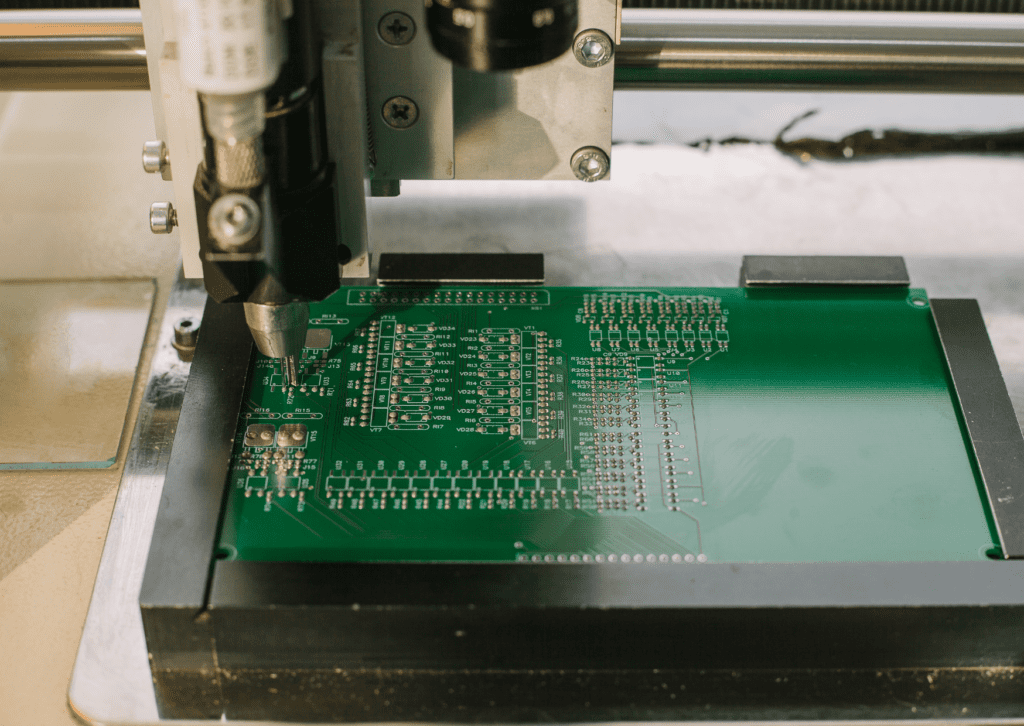
Configure to Order (CTO) is a manufacturing process in which a product is assembled to customer specifications. Customers select from a range of options when ordering the product, and the finished product is then created using the customer’s chosen configuration.
This process begins by closely understanding and documenting customer requirements to ensure the final product precisely aligns with what the customer envisioned. CTO is a variation of the make to order production strategy, primary process where products certain components are manufactured only after a customer order is received.
Benefits of CTO in Manufacturing Efficiency
This allows manufacturers to offer a wide range of configurable products without needing to keep all variants in stock, as each product can be customized to meet the customer’s specifications through the configure to order process, which leverages existing building blocks to create custom made products.
The configure to order approach streamlines the production process by allowing manufacturers to assemble complex products, based on specific customer requirements. Configure to order also enables more efficient inventory management, storage capacity, as manufacturers can produce components in bulk and assemble them as needed based on customer orders. The manufacturer produces components using a configure-to-order system, balancing demand with production capacity to ensure efficiency and reduce waste.
Optimizing for Today’s Competitive Market
In today’s competitive market, the main difference between CTO and traditional manufacturing lies in how inventory costs are managed and reduced. By sourcing inventory only as needed and producing a customized product to meet exact specifications, manufacturers can avoid the overhead associated with pre-made, general market products. This tailored production model not only aligns better with customer demands but also enhances the company’s ability to manage resources more efficiently.
A configure to order CTO system enables manufacturers to align component production with demand, optimizing efficiency and minimizing waste.
The Advantage of Configure to Order Manufacturing
In addition, configure to order CTO manufacturing processes can help reduce costs by allowing for mass production of standard components that can be used in various configurations to certain specifications. Configure to order CTO manufacturing allows for a high degree of customization while maintaining the efficiency of mass production processes, which is essential for meeting diverse market demands.
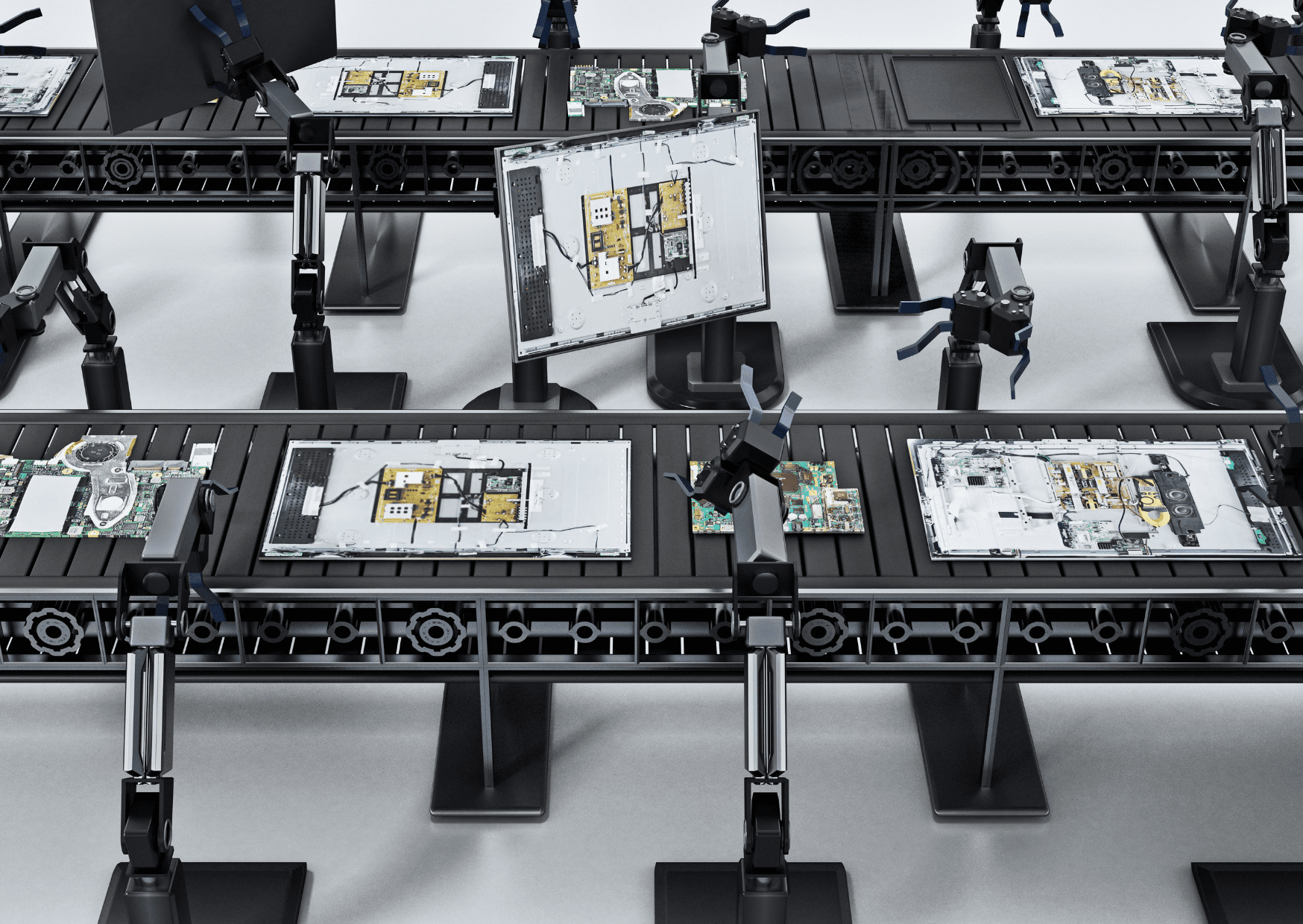
As a result of definite advantages, configure to order CTO is an increasingly popular manufacturing strategy for companies that offer customizable products.
Unlike traditional make to order, where every component belongs each product is built from scratch, configure to order CTO allows for the mass production of standard components that can be used in configurable products in various possible configurations. As a result, configure to order is an increasingly popular production process for companies that offer customizable products. By focusing on customer requirements, CTO enables manufacturers to design products that are not only versatile but also directly targeted to meet the market’s current demands.
The Benefits of CTO
This type of customization through configure to order offers several benefits for both businesses and consumers. For businesses, configure to order CTO allows for greater production flexibility and the ability to respond quickly to changing customer demand.
In addition, CTO can help companies to better manage inventory levels, reduce waste, and optimize their supply chain by leveraging the configure to order approach. Effective inventory management and supply chain optimization are crucial for businesses implementing configure to order, as it helps optimize stock levels and reduce carrying costs.
Furthermore, configure to order products can help to reduce environmental impact by reducing the amount of material and energy required to produce each unit through its customized manufacturing process. Ultimately, using configure to order products is a win-win solution that can benefit businesses and consumers.
Moreover, by reducing excess inventory, configure to order can help lower inventory carrying costs, which can be a significant expense for manufacturing businesses. The adaptability of the CTO model means that it can rapidly adjust to new or changing customer requirements, providing a significant competitive edge.
How does Configure to Order (CTO) work in the manufacturing process?
Understanding the Configure to Order Production Process
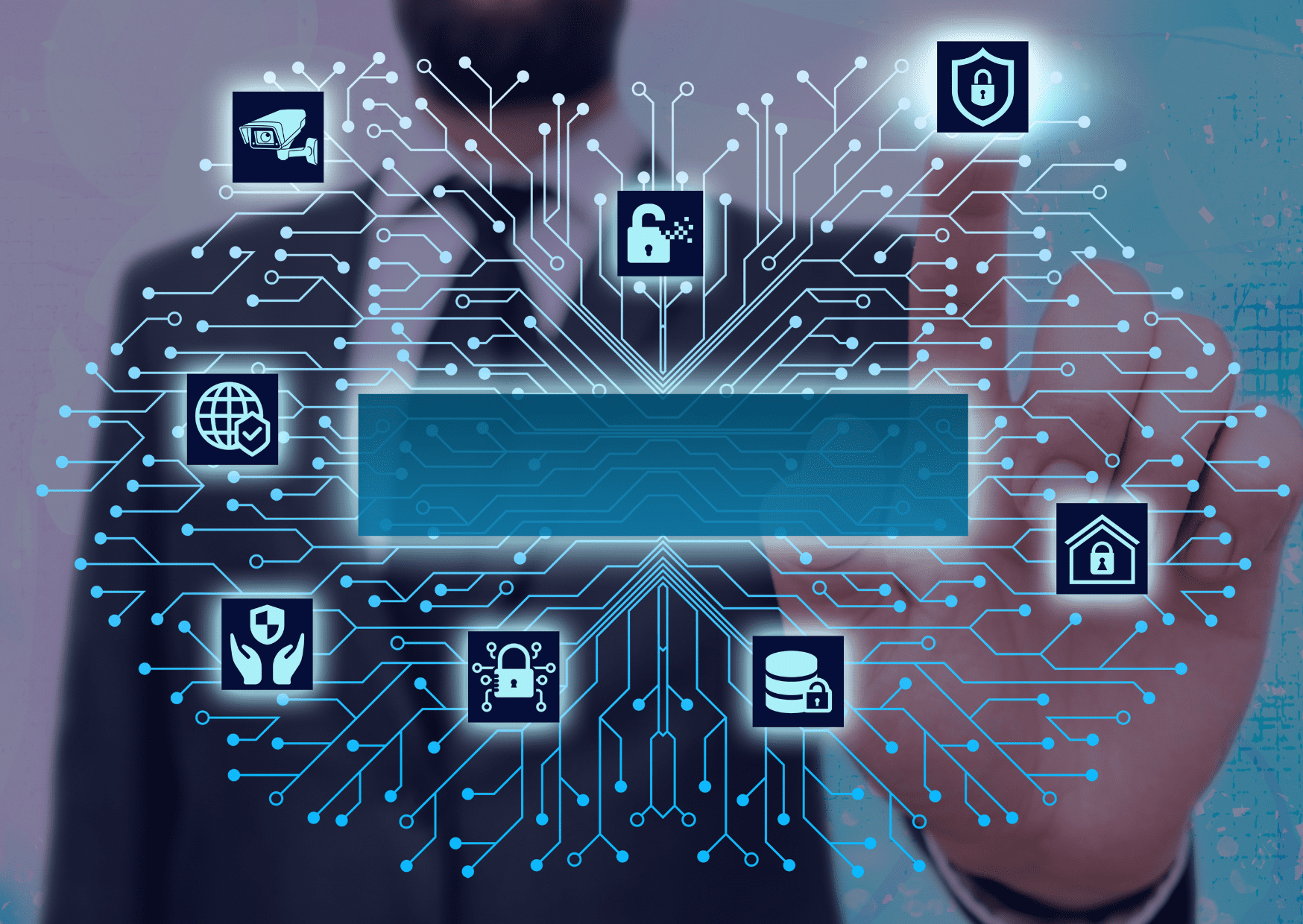
Configure to Order (CTO) is a mode of CTO manufacturing in which a product goes through final customization steps typically at the end of the manufacturing process to complete the build to a predetermined order and specification.This approach allows for greater flexibility in the supply chain, as manufacturers can respond quickly to changing customer demands.
This make CTO process differs in depth knowledge how manufacturer builds it from the make to order approach, where the entire product is built from start to finish based on a customer order. The entire CTO process is designed to be responsive and efficient, ensuring that customer requirements are met swiftly and accurately from the initial order through to final assembly.
Implementing the Configure to Order Process for Various Products
This configure to order manufacturing approach can be used for a wide variety of products, from computers to cars. By leveraging CTO, companies can streamline their supply chain and reduce lead times, as they can produce standard components in bulk and customize them as needed based on customer orders.
While make to order is suitable for highly customized products, configure to order offers a more streamlined approach for products with a set of predefined options.
Another approach to configure to order is to make component or hardware changes in the final stages of the final product assembly process that will change the product features or performance based on customer satisfaction with the product configuration selected.
As a result, customers can order products that are better suited to their needs and preferences thanks to the configure to order manufacturing methodology. By considering customer preferences, CTO manufacturing enables businesses to create products that better satisfy their target market.
In some cases, companies may also utilize an engineer to order approach, where products product solutions are designed and engineered from scratch based on customer specific product and customer requirements.
How can you make the most of CTO in your business?
Undoubtedly, configure to order can be a great way for a manufacturing business to streamline its operations and make the most of its resources. By streamlining departments and improving communication between sales reps and production teams, configure to order can help businesses create custom made products more efficiently.
Training sales representatives to deeply understand the configure to order process ensures they are well-equipped to address potential customers’ questions and tailor solutions to their specific needs.
But how can you ensure you’re getting the most out of configure to order in your own company?
Developing persuasive sales pitches that effectively communicate the benefits of CTO manufacturing can significantly enhance customer understanding and drive higher conversion rates.
Here are a few tips:
Configure to order can be more efficient and easier sales, than make to order for businesses offering products with a limited set of customization options.
First, when implementing configure to order, determine with your customer the variants that will be doing precisely what is required and establish firm specifications for each configuration, including the testing required at the end of the final assembly and pre production process to ensure the product meets the specific customer requirements. This establishes the levels of customization needed for configure to order and defines each product to be offered.
Having a well-defined process in place ensures that the manufacturing team can quickly and efficiently configure the product once an order arrives, reducing lead times and improving customer satisfaction.
Second, to enable configure to order, create robust processes for receiving, storing, and imaging the range of software or firmware variants that will be used to meet the customer’s specifications for custom made products. Ensure product nomenclature and revisions are clear and tightly aligned with the Bills of Materials for components and assembly instructions to ensure the correct product configurations match the customer order and are therefore built correctly on the manufacturing floor through the configure to order process.
Third, implement robust inventory management practices when terms configure to order to ensure that you have no excess inventory of the right components and materials available when needed. This can help prevent delays in the configure to order process and improve production plan overall efficiency. By doing so, and by implementing effective inventory management practices, you’ll be sure to get the most out of this powerful configure to order tool.
Finally, keep in mind that configure to order is not a one-size-fits-all solution. Every business has different needs and supply chain constraints, so it’s essential to tailor configure to order to fit your company’s particular requirements. By aligning your CTO strategy with your overall supply chain management approach, you’ll be sure to get the most out of this powerful configure to order tool.
Frequently Asked Questions about Configure to Order (CTO)
1. What is Configure to Order (CTO)?
Configure to Order (CTO) is a manufacturing process where a product is assembled to customer specifications. Customers select from a range of options when ordering the product, and the finished product is created using the customer's chosen configuration.
2. How does the configure to order manufacturing process work?
The configure to order process begins by understanding and documenting customer requirements. Components are produced in bulk and kept ready for final assembly. Once a customer configures the product, the manufacturer produces the configured product according to the selected specifications, leveraging existing building blocks to create custom made products.
3. What are the advantages of configure to order (CTO) manufacturing?
The advantages include improved production efficiency, better inventory management, reduced waste, and the ability to offer a wide range of customizable products. CTO manufacturing emphasizes customization over mass production, allowing manufacturers to meet specific customer preferences and reduce inventory costs.
4. How does CTO differ from make to order and make to stock?
Unlike make to order, where the entire product is built from scratch based on customer orders, and make to stock (MTS), where identical products are produced and stored in anticipation of demand, CTO uses pre-manufactured components to assemble products based on specific customer configurations, balancing the efficiency of mass production with the flexibility of customization.
5. What role does inventory management play in CTO manufacturing?
Effective inventory management is crucial in CTO manufacturing. It involves sourcing inventory only as needed, maintaining the right components in stock, and ensuring that the manufacturing process aligns with customer orders. This helps in lowering inventory costs and optimizing storage capacity.
6. How can enterprise resource planning (ERP) systems support CTO processes?
ERP systems integrate various business processes, including inventory management, production planning, and sales. In a CTO environment, the manufacturer's ERP system helps streamline the configure to order process by coordinating components, tracking customer orders, and managing production schedules to ensure timely delivery of customized products.
7. Can you provide examples of organizations using CTO manufacturing?
Examples of organizations using CTO manufacturing include custom clothing vendors like screenprinting and custom clothing shops, contract manufacturing companies, and manufacturers of sports equipment such as golf clubs, tennis rackets, and hockey sticks. These companies use CTO to offer products with features e.g., drawers, doors, or specific performance characteristics tailored to customer requirements.
8. What are the technology requirements for configure to order manufacturing?
Key technology requirements include a robust ERP system, product configurators, and potentially CPQ (Configure, Price, Quote) software. These tools help manage the complex process of customizing products, from configuring specifications and features to ensuring the correct components are available for final assembly.
9. How does CTO manufacturing handle quality assurance?
In CTO manufacturing, testers perform quality assurance at various stages of the production process to ensure that the final product meets the specified customer requirements. This includes verifying that the assembled product matches the chosen configuration and conducting functional tests to confirm performance.
10. What are some best practices for implementing CTO in a business?
- Best practices include:
- Developing clear processes for customization and final assembly.
- Training sales reps to understand the configure to order process and effectively communicate its benefits.
- Using ERP systems to streamline operations.
- Implementing robust inventory management practices to prevent delays.
- Aligning the CTO strategy with overall supply chain management.
- Leveraging product configurators to allow customers to visualize and customize products easily.
By following these practices, businesses can effectively implement CTO, enhancing their ability to meet customer demands while optimizing production efficiency and reducing costs.