Engage Early and Often
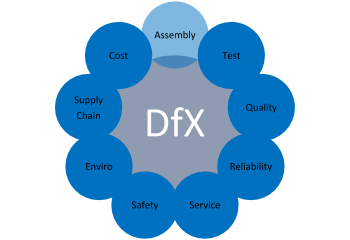
Early involvement is better. That’s a universal truth that applies to almost any situation we can think of. It holds especially true in today’s electronic manufacturing market place. With the explosion of IoT, sensors, cloud communications, global supply chains, and enormously large buyers like Google & Amazon, it is more imperative to scrutinize a new product in the design and quoting stages. Design for Excellence (DfX) has many elements that comprehensively examine a product from many angles with the goal of making improvements as early as is possible.
In 1991, Clark & Fujimoto stated what is now a widely accepted principle: 80% of the manufacturing cost of a product is determined by the design of the product. The cost of making a design change rises exponentially as time elapses and a product moves from concept to prototype, to volume production. Therefore, applying the relevant elements of DfX as early as possible will pay large dividends in controlling costs and shortening the time to market.
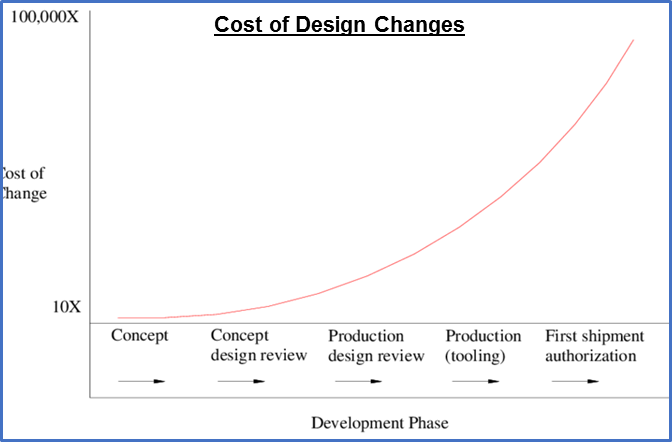
The reality of product development is each project is at a specific point in time, and everyone involved wants to produce a very high-quality result that is most efficient. At Vergent, we oftentimes receive an existing design and we apply DfX principles in the quoting stage before we get to First Article unit builds. The most common elements we use with clients are as follows:
- Supply Chain DfX – we utilize artificial intelligent supply chain algorithms to assess risk and supply constraints of all electronic components on the Bill of Materials. It’s important to determine any high-risk components and any not recommended for new designs (NRND) and implement alternatives to derisk supply.
- PCBA level DfX – common issues we see that need to be addressed prior to First Article build include bridging, thermal balancing, polarity, pad size and spacing, and component density.
- Final Assembly level DfX – common issues to resolve early include assembly tolerances & fit, part orientation, assembly operator & tool accessibility, adhesive use, fasteners, and torque standardization.
- Test development DfX – often overlooked, test development is key. We evaluate and help resolve issues like the availability of critical test nodes, buried components, test coverage, and order of testing.
Whatever stage your project is at, always remember early involvement is better.