The electronic product development process is a structured approach to transforming an idea into a market-ready product. Whether you’re developing medical devices, aerospace components, or industrial electronics, a well-defined process ensures quality, efficiency, and compliance with industry standards.
This guide outlines the key stages of electronic product development, addressing best practices, potential challenges, and strategies for success.
Key Stages of Electronic Product Development
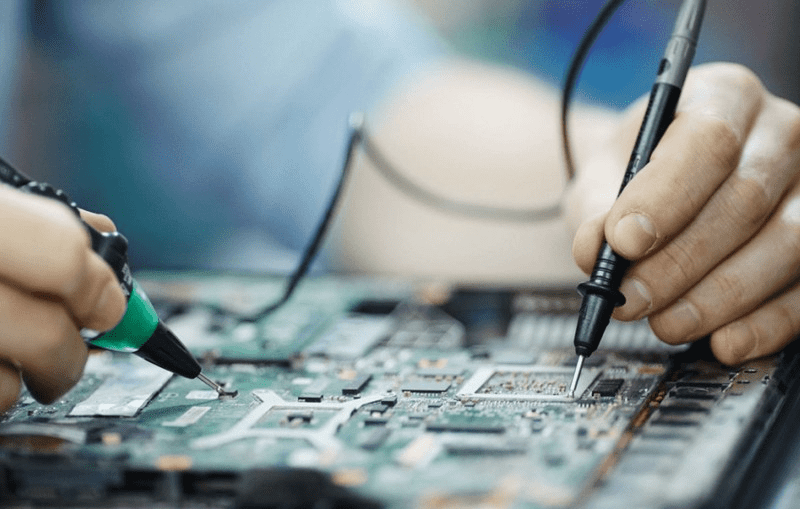
Technician testing a circuit board using probes for diagnostics and troubleshooting in electronics manufacturing.
1. Idea Generation and Feasibility Analysis
The process begins with idea generation, where market needs are identified and potential solutions are brainstormed. Feasibility analysis helps determine whether the concept is viable from technical, financial, and regulatory perspectives.
Key activities:
- Conducting market research
- Evaluating technical feasibility
- Performing cost-benefit analysis
- Reviewing regulatory requirements
Best practices:
- Engage stakeholders early to validate demand
- Conduct SWOT analysis to identify strengths and weaknesses
- Utilize rapid prototyping tools to validate concepts (prototyping is a critical stage in the electronics product design and development process )
2. Requirement Definition
Once the concept is deemed feasible, product requirements are defined to outline functional, technical, and regulatory needs.
Key activities:
- Developing a Product Requirements Document (PRD)
- Setting performance specifications
- Establishing compliance requirements (e.g., ISO 13485 for medical devices)
- Identifying potential risks
Best practices:
- Collaborate with cross-functional teams
- Use requirement management tools for tracking changes
- Prioritize requirements based on feasibility and market demand
3. Concept Development and Prototyping
Concept development involves creating initial design phase and developing prototypes to test the product’s feasibility.
Key activities:
- Schematic design and PCB layout
- Component selection and sourcing
- Building prototypes using 3D printing or CNC machining
- Conducting preliminary tests
Best practices:
- Follow an iterative approach to prototyping
- Use simulation software for design validation
- Work closely with suppliers to ensure component availability
4. Detailed Design and Engineering
The prototype evolves into a fully functional product through detailed design, ensuring manufacturability and compliance.
Key activities:
- Finalizing electronic circuit designs
- Developing embedded software and firmware
- Optimizing the design for manufacturability (DFM)
- Preparing detailed documentation
Best practices:
- Conduct regular design reviews
- Implement design for testability (DFT)
- Utilize version control for design files
5. Testing and Validation
Rigorous testing ensures the product meets performance and regulatory standards.
Key activities:
- Functional and performance testing
- Electromagnetic compatibility (EMC) testing
- Compliance certification (e.g., FCC, CE, UL)
- Environmental and stress testing
Best practices:
- Develop comprehensive test plans
- Automate testing where possible
- Address failures through root cause analysis
6. Manufacturing and Production
After successful validation, the product moves into production, focusing on scalability and quality control.
Key activities:
- Selecting manufacturing partners
- Setting up quality assurance processes
- Conducting pilot production runs
- Implementing paperless MES systems
Best practices:
- Choose manufacturers with relevant industry experience
- Conduct regular audits to ensure compliance
- Optimize supply chain logistics
7. Product Launch and Market Entry
Product launch involves marketing strategies, distribution planning, and post-launch support.
Key activities:
- Developing a go-to-market strategy
- Establishing distribution channels
- Preparing user documentation
- Collecting initial market feedback
Best practices:
- Implement a phased rollout strategy
- Monitor market performance
- Use digital marketing for broader reach
8. Post-Market Support and Sustaining Engineering
Ongoing support and updates are essential to maintaining product relevance and customer satisfaction.
Key activities:
- Providing technical support
- Managing firmware updates
- Handling product returns and repairs
- Gathering user feedback for improvements
Best practices:
- Implement reverse logistics strategies
- Monitor industry trends for innovation opportunities
- Stay compliant with evolving regulations
Common Challenges in Electronic Product Development
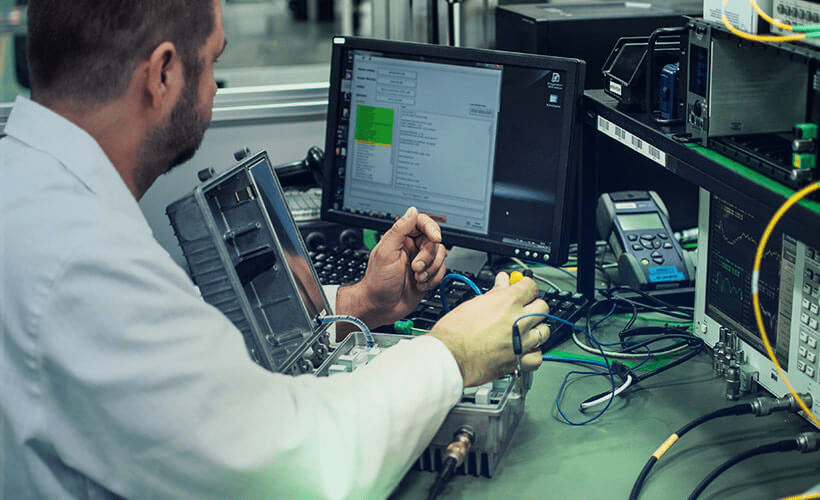
Engineer testing and analyzing electronic equipment using specialized software and diagnostic tools in a lab setting.
Despite following a structured process, challenges are inevitable. Some common obstacles include:
- Rapid technological changes – Staying updated with emerging technologies can impact timelines.
- Regulatory compliance – Meeting international standards can be complex and costly.
- Supply chain disruptions – Component shortages or delays can affect production schedules.
- Cost management – Balancing costs while maintaining high-quality standards is critical.
Strategies for Success
To overcome challenges and ensure a seamless development process, businesses can adopt the following strategies:
- Agile methodologies – Iterative development allows flexibility and quick adjustments.
- Digital twin technology – Virtual simulations help test and refine designs before production.
- Collaborative partnerships – Working with experienced suppliers and manufacturers reduces risks.
- Automation – Automated testing and production enhance efficiency and accuracy.
Conclusion
The electronic product development process is a complex yet rewarding journey that requires careful planning and execution. By following a structured approach, businesses can achieve high-quality products that meet customer needs and industry standards.
Partnering with experienced design and manufacturing firms like Vergent Products can help navigate these challenges and bring innovative products to market efficiently.
Looking to bring your electronic product idea to life? Contact us today to explore our comprehensive product development solutions.
Frequently Asked Questions (FAQ)
1. What is the electronic product development process?
The electronic product development process is a structured approach to transforming an idea into a market-ready product. It involves stages such as idea generation, feasibility analysis, requirement definition, concept development, prototyping, detailed design and engineering, testing and validation, manufacturing, and post-market support.
2. How long does it take to complete the electronic product development process?
The timeline for electronic product development varies based on factors such as product complexity, regulatory compliance, and design iterations. On average, the process can take anywhere from six months to two years, depending on the number of prototyping cycles, testing phases, and manufacturing readiness.
3. What are the biggest challenges in the electronic product development process?
Key challenges include rapid technological changes, ensuring regulatory compliance (such as ISO 9001:2015, ISO 13485 for medical devices, and AS9100 for aerospace), managing component obsolescence, mitigating supply chain disruptions, and balancing cost management while maintaining product quality.
4. What are the benefits of using a paperless Manufacturing Execution System (MES)?
A paperless Manufacturing Execution System (MES) improves production efficiency by reducing errors, enhancing traceability, and ensuring real-time data tracking. It supports compliance with industry standards such as ISO 9001:2015 and facilitates scalability in high-volume contract manufacturing.
5. What regulatory certifications are required for electronic products?
Common regulatory certifications include ISO 13485:2016 for medical devices, AS9100D for aerospace products, and ISO 9001:2015 for quality management. Additionally, compliance with FCC, CE, and UL standards may be required depending on the target market and product application.
6. Why is prototyping important in electronic product design?
Prototyping is crucial in electronic product design as it allows for the validation of product concepts, testing of functional performance, and identification of potential design flaws. It enables iterative development, reduces development costs, and accelerates time-to-market.
7. What factors should be considered when selecting electronic components for product design?
When selecting components, considerations include performance specifications, regulatory compliance, supply chain availability, cost-effectiveness, and manufacturability. Choosing components with long lifecycle availability and RoHS compliance can prevent issues during production.
8. How does Configure-to-Order (CTO) impact electronic product development?
Configure-to-Order (CTO) allows customers to customize products based on specific needs while maintaining efficient manufacturing processes. CTO enhances operational efficiency by leveraging modular designs and flexible manufacturing strategies to meet diverse market demands.
9. What is the role of reverse logistics in electronic product development?
Reverse logistics plays a critical role in managing product returns, refurbishments, and end-of-life recycling. It ensures compliance with environmental regulations, enhances customer satisfaction, and contributes to sustainable business practices.
10. How can contract manufacturing improve electronic product development?
Contract manufacturing provides scalability, expertise, and cost-efficiency in electronic product development. It allows businesses to focus on innovation and market strategies while leveraging the capabilities of certified manufacturers with experience in precision manufacturing and regulatory compliance.